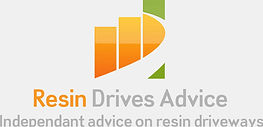
Typical Problems Due to Poor Installation
Below are some of the typical mistakes that contractors can make when installing your resin bound surface. Take a look through the images and the best ways to ensure that these issues are avoided during the installation.

Resin Bound Surface not Installed at Correct Depth

How to Avoid
Most resin driveways should be installed at a depth of 15mm as a minimum. The above photo shows a driveway installed at around a 5mm depth, this can lead to problems such as patches of the resin lifting and cracks forming in the resin surface.
You should ask the contractor at what depth they intend to install the resin bound system, as the product is hand laid there will be always small variations in depth however it should always be at least 15mm at the lowest point
If your installation is taking place on a patio or pathway a typical resin bound system can be installed at a 12mm depth. This is becasue of the reduced weight being placed on the surface which reduces the chance of movement.
Problem With Your Resin Driveway?
Not sure what to do?
Have a look at our independant advice on what the best ways to contact your installer and what they should be doing to rectify the problem....
How do I choose a contractor I can trust?
This website is full of information on what to look our for when deciding on getting a resin bound driveway. Take a look at some of the key tips to look out for when choosing a resin bound installation company...

Resin Bound Surface Crack
How to Avoid
Most cracks appear in a resin surface appear due to poor resin materials being utalised by the contractor or by not mixing the resin with the reccomended amount of stone.
Most resin suppliers reccomend that each of their resin kits are mixed with 100kgs of stone. This 100kgs is usually made up of a mixture of 75kgs of 2-5mm sized stone and 25kgs of 1-3mm.
The exact speficiation can change depending on the resin manufacturer therfore you should ask your installer to see the data sheets of the resin to check that they are installing as per the guideline of the manufacturers.


Resin Bound White Patch

How to Avoid
White patches can form on a resin surface after the installation due to moisture being present as the resin was curing. This happens because the water produces small air bubbles in the resin and can sometimes appear several weeks after the install takes places.
Your contractor should be using kiln dried aggregates to mix with the resin materials from a reputable supplier to ensure that no mositure is present in the stone. The stone should be kept covered if staying outside before the installation takes place and the surface should be completley dry before the resin mixture is trowelled into place.
The setting times of resin bound surfaces change depending on the ambient temperature. This will mean that the contractor needs to choose a dry day to start the resin bound installation and that the weather needs to stay dry for around 4 hours after the install is complete.

Resin Bound Colour Change
How to Avoid
There are two main types of resin that are used for resin bound surfacing, aliphatic and aromatic. These are commonly know in the industry as UV stable and Non-UV stable.
The Non-UV stable resins are typically used with golden coloured stones and will change to an amber colour after the install has taken place. This doesn't usually cause a problem and can complement the final look of the resin driveway, pathway or patio.
If you have chosen a black, silver or beige coloured stone you will need to ensure that the contractor uses the UV stable resin to avoid any colour change in the final surface. The image to the right shows a sample of the stone when mixed with a UV resin ontop of a driveway that has been installed with standard resin.
The cost of UV stable resin is around £5/m2 more and will be reflected in the cost of your driveway however prevention is better than the cure!


Resin Bound Breaking Up

How to Avoid
Holes that appear in a resin bound surface can be caused by several factors. The most common factor is movement in the sub-base which origionally causes a crack that further expands.
Another common reason for the resin surface to start breaking up is that the contractor has used inferour resins or has mixed too much stone with each resin kit which has weakened the final surface.
It is important that a "forced action mixer" is used to mix the resin and stone materials. This is different to a cement mixer as it gives an even blend of materials. A cement mixer can often leave "dry spots" giving an uneven mixture of resin and stone which can cause the surface to break up after installation.
Most suppliers reccomend that a priming agent is used when installing the surface onto a concrete base which is roller applied to the concrete before the installation starts. By not using the primer, delamination can occur between the resin bound surface and the concrete which can cause the material to break up.

Resin Bound With Joints
How to Avoid
Resin bound driveways are installed as a continious seamless surface however in high temperatures if the contractor isn't working quickly enough lines can appear in the final surface.
These lines often appear as the batch of resin that has been trowelled has set before the next batch has been connected to it. Unfortunatley once this has happened there is no way of rectifying the problem apart from relaying the full driveway.
This problem is rare as tempeatures in the UK rarely reach 25C which is usually the point at which the working time of the resin reduces. The type of resin that the contractor uses can effect the amount of working time they have with the materials so ensure they are using a reputable supplier before the work starts.


Resin Bound With Stripes

How to Avoid
Stripes in a resin bound surface are usually caused by a changes in colour between the different mixes of resin that have been laid.
This can be avoided by ensuring that the each mixture of resin and stone are rotated in the mixture for 3 minutes for each batch. If one batch of stone is left in the mixer for longer than than another, the resin materials can start to absorb into the stone and create a colour change in the finish.
If you're watching your resin install take place, it's worth noting that how you see the driveway during the install is exactly how it will set!
Colour change can also be avoided by mixing the stone without the resin for one minture to remove any dust from the stone.

Resin Bound With Sub-base Movement
How to Avoid
Installing onto a sub-base such as block paving or paving slabs can often lead to movement in the subase which can cause an uneven finish in your final resin bound driveway.
A typical new sub-base would comprise of 6 inches of an MOT followed by 2 inches of base coat tarmac. Don't forget to ask your installer what they are intending to install to avoid any problems with movement.

>> Dont let us scare you! Most of the examples above are extreame cases and most installers have plent of experience in installing resin bound surfaces <<
Need a trusted installer?
Fill out the form below and we will pass your details to a trusted install company in your area.